
Studio S
P O T T E R Y
WELCOME!
Scroll Down For Additional Information
Dairy Barn Becomes Home for Crafts
by Bill Lewis
Accent Staff WriterDaily News Journal Accent - November, 1981




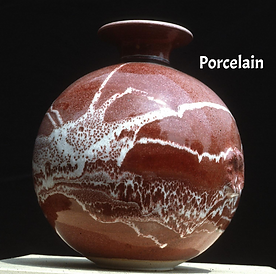

Most people remember playing with clay as children, but the substance children mold into various shapes for fun can also be turned into beautiful and functional artworks.
That happens on a daily basis at Studio S Pottery, 1426 Avon Road, where Lewis Snyder, a master potter, and several interns create unique clay pieces.
Clay, and what they can make it into, clearly fascinates them. So much so, in fact, that students have come from all over the country to study at the studio Snyder carved from an old dairy barn.
"Back when I was teaching (at MTSU) there was no place for students to get practical experience. If you're seriously going to work at it as a professional, then you need to get some practical experience," said Snyder, explaining why his is one of the few studios that take interns.
During the two years he asks them to stay, they are involved in marketing finished pieces, which are displayed in two galleries, do technical work with clay and eventually, develop their own styles.
It all happened somewhat accidentally, noted Snyder.
In 1968 he decided he needed a place to get away from the pressures of teaching at the university and concentrate on his art. The old shell of a dairy barn seemed the perfect place. "But I didn't have a barn or anything like that in mind," said Snyder, who also designed the bottom level of the MTSU dairy barn.
The job of remodeling the barn to create a studio was a job he readily accepted, but it was a tremendous challenge.
"I had an uncle come down from West Virginia to help me for six months. He stayed seven years," he said. The renovation and repairs were so complete that the only original parts are the building's tin roof and the hayloft floor.
It evolved into what it is now," said Snyder, who admitted an affinity for old dairy barns.
Now the barn is being put to a less traditional but more productive use. Instead of the rustle of hooves on straw can now be heard the spinning of the potter's wheel and the roar of the kilns used to make the pottery.
The old silo itself now houses a large kiln instead of silage for farm animals.Snyder is still busy expanding the studio's capabilities. Five kilns stand inside and two more are outside, and he is laying the foundation for another kiln room.
He also has added new rooms, a deck in the rear and a woodshop behind the second floor gallery. The third floor is used for storage.
A water fountain in back completes the transformation of a barn into a rustic-looking studio located in a quiet residential area.
Like his studio, Snyder's technique in creating art from clay also is a combination of the old and the new, the traditional and the modern.
The kilns are gas and electric, taking advantage of modern convenience and technology to produce perfect pieces.
Temperatures achieved inside a kiln are all-important, since they determine to a great extent the quality and the type of piece produced.
"We fire everything twice," said Snyder.
First, he and his students bisque fire the pieces to dehydrate them, he said. For that to be successful, temperatures inside the kiln must range from 1,850 to 1,900 degrees."We glaze from 2,300 to 2,325 degrees," he said.Those temperatures create stoneware. The studio also fires some porcelain, he added.
Various techniques in use of the kiln give different results. Reduction firing, in which limited amounts of oxygen are allowed inside the kiln, give the clay and the glaze a chemical bond and brings out a new spectrum of color.
Potters cannot control oxygen levels in electric kilns, which give a glaze that looks like a coat of paint, said Snyder.
Use of a salt kiln gives a unique result. Liquid clay with a colorful oxide is placed inside the kiln, which is fired to 2,300 degrees. No glazing takes place. When the kiln is at its hottest, the craftsman pours in pounds of rock salt, which vaporizes."It's like a heavy fog, and as the fog settles, it settles on everything in the kiln, giving color and texture," said Snyder.
The technique was especially popular from Civil War days until the turn of the century, he added.Modern technology provides the ability to produce perfectly fired pieces, but there is something it cannot provide -- the craftsmanship required to turn ground, dry clay into functional art.
Throwing a piece is a learned skill. The craftsman must hold his hands perfectly and center the clay. Taking function and aesthetics into consideration, he or she then can use a "trim tool" with a ribbon blade to cut away excess clay on the bottom and give a pot a "footing," he said.
Years of study, experience, dedication and hard work are often required before a novice develops a worthy style.The result is artwork so beautiful that one of Snyder's designs was purchased by Jimmy Carter for use in the White House while he was president.
And the crafts are in demand in other parts of the country as well."We sell to eight or ten shops across the country. We have gifts going all over the globe," said Snyder.
Snyder said he holds classes as a community service. One of his students told him she plans to become a professional after her husband finishes school, and another said he will use his skills following his retirement. He also has allowed group tours of the studio which he said is "not a typical production shop" since each piece is unique. He plans an open house November 21-22.
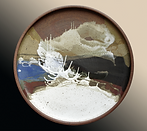
Lewis & Eric Snyder